Self-build timber-frame homes from the show
Discover more about the benefits of this build method through these inspiring projects.
There are many reasons to opt for building your own home with a timber frame. Opting for off-site construction offers precision and often a faster build time. It can be an eco-friendly method. Most affordable kit homes are timber frame construction. Often, craftsmanship comes into play.
Many Grand Designers have been motivated by these objectives and have taken one or other of these routes with stunning results. Discover more about the benefits of self-build timber-frame construction through these inspiring projects.
Low-cost family home
When Steph Wilson secured a plot of land on her grandfather’s old farm for a self-build project, she set her heart on an earth shelter-inspired house. But, with the probable cost reaching an unaffordable £500,000, Steph and her husband Alex had to revise their plans. As part of the cost-savings, the couple chose an economical timber-frame build. This helped towards creating a family home with generously-sized living spaces for just £270,000. The build took just 10 months to complete. As the house has a high level of insulation, its running costs will be low.
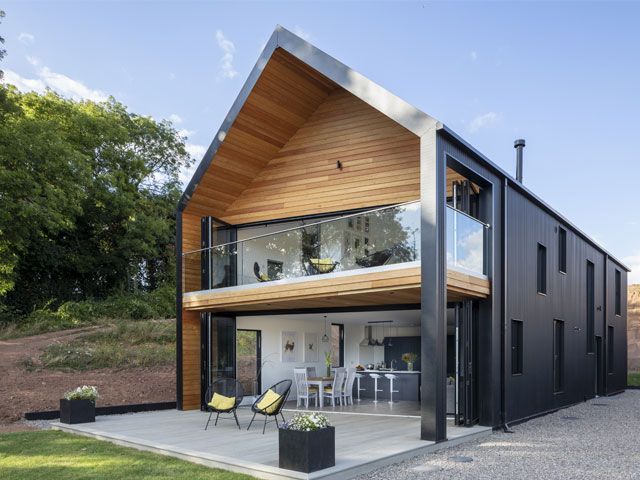
The two-storey, three-bedroom house is a small budget success. Photo: Mark Bolton
Sustainable greenbelt house
Builder Paul Rimmer spent his career constructing homes with bricks and mortar. But when it came to building a new home on land opposite the farmhouse he restored, it was time for a different approach. The land was a greenbelt site and Paul was first told he had no chance of gaining planning permission. But approval came in the space of two years thanks to the zero-carbon, self-build timber-frame design.
Stringent building methods and sustainable materials were essential to achieve the super-low carbon emissions. The structure uses 150mm of insulation on every wall with no gaps. Every external wall has a vapour barrier on the inside and a breathable membrane on the outside. Where possible the frame was made by hand on site. It was time-consuming but Paul felt strongly about maintaining the highest quality. The frame itself cost £100,000, less than a quote from a prefabrication company.
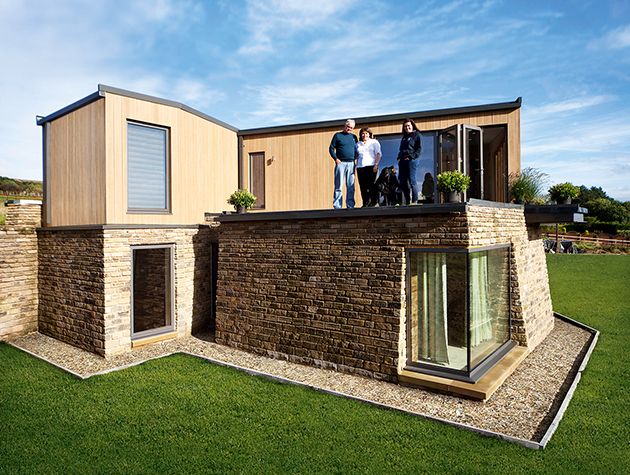
Living spaces are on the first floor, with bedrooms below. Photo: Andrew Wall