Exterior cladding forms the protective external layer of a property, and the choice of material will dictate the finished look.
There’s an array of different cladding types and materials to choose from, including timber planks, composite boards, metal sheeting and stone tiles.
Prices vary between materials, and professional installation adds to the final cost.
Check the regulations
Fitting cladding to the outside of your home may fall under permitted development rights (PDR) if you are replacing worn-out cladding like for like.
But this won’t apply to listed buildings or if you live in a conservation area, a national park or an Area of Outstanding Natural Beauty (AONB), in which case you’ll need to apply for planning permission.
Self-builders must include details of the cladding when making a planning application. In some cases, the materials that can be used will be dictated by the planners to suit the surrounding or neighbouring properties. Contact your local authority for advice before starting any work.
For more information, visit the Planning Portal. The performance of any cladding system must comply with Building Regulations.
In accordance with European Standards EN-13501-1, the fire-rating classification for cladding materials ranges from A1, which means non- combustible and makes no contribution to fire, down to F, which means combustible and easily flammable.
For a home less than 18m in height in England and Wales that’s less than 1m from a boundary, the external surface should be Class B or better. If more than 1m from a boundary, there’s no provision required. In Scotland the requirement is for A1 or A2 no matter how far it is to the boundary.
Check a product’s fire rating, speak to the manufacturer and ask about warranties. It must also be installed correctly.
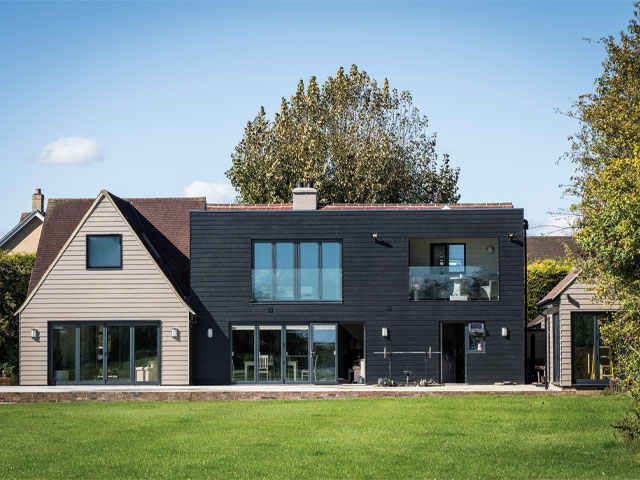
This self-build home features fibre-cement weatherboarding, chosen for its traditional shiplap look and low maintenance. Cedral Lap in grey brown and dark brown from Cedral
Composite options
Fibre-cement board is a manmade cladding that’s recyclable and easy to maintain. Made from cement, cellulose fibres, and filler, it comes as boards, panels or shingles in finishes ranging from smooth to imitations of wood or stone.
‘Fibre cement has a long lifespan and will not warp or rot, plus it has an excellent A2 fire classification,’ says Lisa Grosse of Cedral.
Panels have a fitting system with concealed screws for a sleek finish, while planks, mounted on to battens, can be flush-fitted for a contemporary look or overlapped to give a traditional shiplap look. Fibre cement board costs from £55 per sqm. Made from porcelain, glass, and quartz, Dekton looks like stone.
Manufactured in large-format slabs, it’s much lighter than the real thing, but is strong and resistant to the elements. Slabs are applied to an adhesive cement plaster or fixed to a metal framework. It costs from £400 per sqm.
Millboard is made from polyurethane resin and mineral stone to look like real wood. The brand’s Envello Shadow Line+ boards are Euroclass D fire rated. From £143 per sqm.
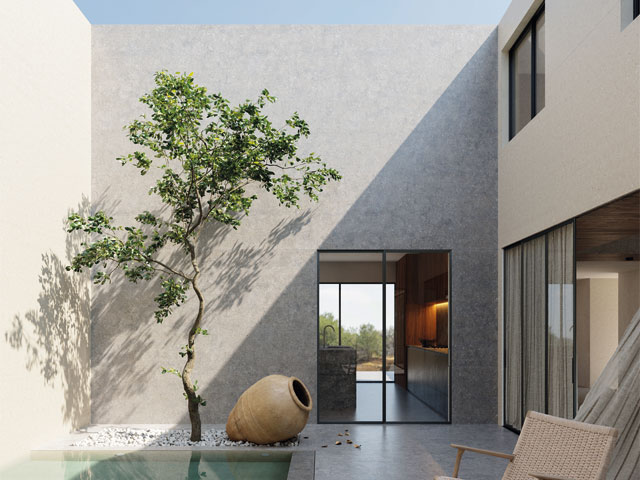
This composite material replicates the look of natural limestone. Dekton Pietrs Koda in Grafite from Cosentino
Make it metal
Aluminium, copper, steel and zinc are all low-maintenance, long-lasting and recyclable cladding options. Lightweight aluminium cladding remains in its original condition for around 40 years, while copper develops a Verdigris patina and has a lifespan of around 100 years.
Steel can be powder-coated in any RAL colour or galvanised and should perform well for around 35 years. Corten steel, also called weathering steel, develops a layer of rust, protecting the metal from further corrosion.
When supplied it looks like sheet steel, but once it’s in place the elements and the rust take hold. Zinc has a shiny surface that develops a patina over time and pre-patinated or pre-pigmented products are available.
Professional installation ensures great performance over the metal’s lifespan. Expect to pay £150 per sqm for zinc or Corten steel and from £275 per sqm for copper.
Tile and brick
Clay tiles for exterior use are available in several different formats and shapes that bring character to any project, from a modern extension to a period home renovation.
They retain colour well and are extremely durable, lasting around 60 years. Machine-made clay tiles cost from £2,000 for 1,000 tiles, or handmade feature tiles will cost around £3,000 for 1,000 tiles.
Brick slips are thin slices of masonry sliced off conventional bricks or purpose made. Available in an array of colours, pre-moulded slips can match most building façades. From £70 per sqm.
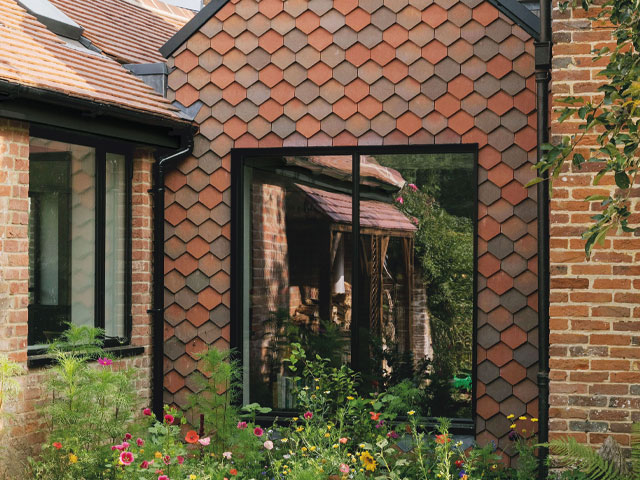
Different coloured clay tiles cover a single-storey kitchen extension to a farmhouse in Farley, Wiltshire. Handmade Arrowhead tiles from Dreadnought Tiles
Natural and treated timber
Take your pick from softwood, hardwood, or modified wood cladding. Planks come in several lengths and widths that are fixed horizontally or vertically using a battening system.
Durable softwood species such as western red cedar, larch and Douglas fir resist moisture and decay, and each offers a different look, from contemporary to country. Hardwoods such as oak and sweet chestnut are more durable than softwoods.
The boards are generally air- or kiln-dried for structural stability and come in rustic or clean-lined finishes. Uncoated timber weathers to a silvery grey or can be given a surface treatment to preserve the original colour, which may need to be repeated periodically.
Heat-treated modified wood has been thermally processed to reduce its moisture content for enhanced stability and durability. Virtually maintenance free with a lifespan of 50-60 years, modified wood has a uniform appearance with few knots.
Choose sustainably sourced timber with FSC certification. Expect to pay from £60 per sqm for softwood, £77 per sqm for hardwood and £100 per sqm for modified timber.
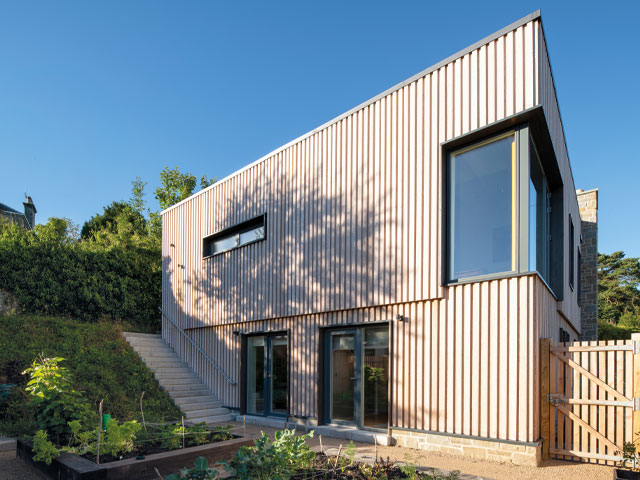
With views across the river Tay to Dundee, Scotland, this three-bedroom home on a former railway embankment is clad in larch boards finished with a wood treatment for an even façade with a weathered appearance. Sila select Siberian larch with SiOO:X Original wood treatment from Russwood.
Silver lining
- Advice on choosing zinc from Jonathan Lowry of VM Building Solutions
- Zinc is shiny but develops a patina when it reacts with rainwater and then with carbon dioxide. After three to ten years an even, middle grey patina is formed, but it takes time for this to become uniform.
- Zinc also comes in a wide range of pre-weathered finishes and coloured finishes where surface tone is created by adding mineral pigments to a durable pre-weathering zinc, which is then sealed with a protective coating.
- When correctly designed and installed, zinc has excellent durability, with a service life of 100 years.
- The most common type of application is standing seam, where wall panels are joined using 25mm-high seams that can be crimped in a single or double lock. The standing seam system can be used on roofs allowing a roof and wall to blend as one.
- Zinc is non-combustible with an A1 fire rating. It’s also low maintenance and corrosion resistant. Because it’s a self-healing metal, scratches on the surface will recover on their own over time.